by Nicholas Stobie
Every pilot flying twins remembers the mantra driven into them during their initial training: Maintain Control, Mixture Up, Pitch Up, Power Up, Gear Up, Flap Up, Dead Leg—Dead Engine, Confirm, Identify and Feather. A plan for the worst, which if executed, should allow you to lumber away to a safe altitude. It’s a clear set of actions rehearsed not only in training but also during the day to day of flying.
Yet when we think about flying singles, we often don’t have the same rigid plan for responding to a power loss after take-off. Pilots are taught to push and hold the nose forward and trim for best glide, but then what? You’ve got 30 seconds until impact. Do you try trouble checks or do you configure the aircraft for the imminent landing? How does this change between airports, aircraft and pilots? This indecision characterises how we place less emphasis on planning for engine failure in singles, despite arguably greater consequences.
Statistically, engine failure is rare. The ATSB’s 2014 investigation into failure rates in piston engine powerplants showed that the traditional Continental and Textron/Lycoming engines had a failure rate of about 13 failures per 100,000 flight hours, with Rotax coming in at a slightly higher 15 per 100,000 flight hours. Move to turbo-prop types and these rates drop further—in 2016, the Pratt & Whitney PT6 family posted a remarkable in-flight shut-down rate of 0.15 per 100,000 flight hours.
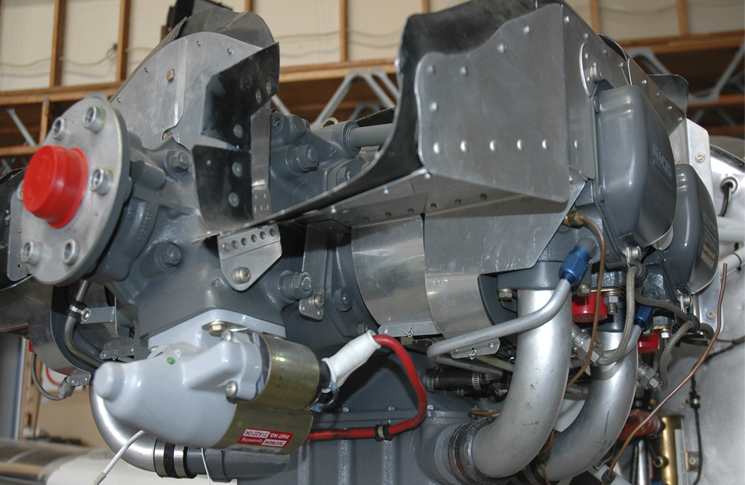
Fatal accident rates also support single engine aircraft being safe and reliable. Reviewing general aviation in the US fleet between 1984 and 2006 (from NTSB annual reviews), the average fatal accident rate of single piston engine aircraft sits at 1.63 fatal accidents per 100,000 flight hours, compared with 1.88 fatal accidents per 100,000 flight hours in their multi piston engine cousins.
Given the comforting statistics for engine failure rates, it’s easy to see how engine failure in singles can be pushed to the very back of one’s mind. However, these statistics bely the consequences of engine failure in singles. Engine failure at any stage of flight exposes the occupants of a single engine aircraft to a subsequent forced landing, with the very real possibilities of serious injury or death. We, as pilots, may be limited in our ability to prevent engine failure, but we have a defining influence on whether that failure leads to a safe landing or a fatal accident.
We all know the basics
If you’ve passed any level of licence, you’ve been taught how to handle engine failure. The specifics vary between types, but generally the doctrine is: maintain control, identify engine failure, conduct critical immediate actions, perform trouble checks which, if unsuccessful, leads into a forced landing procedure.
Most pilots appreciate the need for a pre-flight inspection, and by closely examining your engine you guard against it failing in flight. Leaks, fuel contamination, physical damage, corrosion, unusual noises and excessive oil consumption are all signs that everything is not well ahead of the firewall and that a failure may be imminent.
In training, you also learned flight planning strategies to mitigate the consequences of engine failure: avoid where possible overflying extensive areas of terrain unsuitable for forced landing. Minimise overwater legs by taking the shortest route between land masses. Carry survival equipment, an ELT, life jackets and signalling equipment when required by CAO 20.11.
These basics form the due diligence that pilots are expected to perform for every flight. An average pilot with no experience beyond their bare licence should be capable of all the above. Likewise, the above is designed to be handled by the average pilot with no experience. I would argue, though, that most pilots strive to go beyond just the basic standard, and there are many additional steps you can take to protect yourself when placing all your faith in four or six cylinders.
Plan if and when to turn back
Something that should have stuck from basic training was that you should never turn back following engine failure immediately after take-off. There’s good reason for this lesson—countless fatal accidents have involved pilots unsuccessfully attempting to turn back to the airport following an engine failure on upwind at low level. It’s often labelled the impossible turn, and it’s a procedure fraught with risk.
At some point after departure though, returning to the airport is the safest option. A concept many single-engine operators use is a minimum turn-back height, which serves as a decision point within the take-off safety brief. The time to decide this is before take-off.
The minimum turn-back height splits a take-off safety briefing into three parts:
- An event (engine failure or otherwise) before rotation, necessitating stopping/preparing for an overrun.
- Engine failure between rotation and turn-back height, where you accept the off-airport landing and focus on preparing for that (choosing the most suitable area and configuring for the slowest landing and impact possible).
- Engine failure above turn-back height, where you focus on a steep turn back and maximising glide performance to make it back to the airport.
A clear, defined plan removes indecision under pressure. You either are above or below your turn-back height; there’s no grey area. Formalising the decision relieves the temptation to attempt the impossible turn, and conducting a structured take-off safety brief diminishes the startle effect by placing the immediate actions in the forefront of your mind.
There are many considerations for nominating a minimum turn-back height—your abilities as a pilot, aircraft characteristics, wind direction and runway length, to name a few. An instructor familiar with your circumstances will be able to give you guidance here. Better yet, a dual training flight specifically on engine failure after take-off will allow you to determine exactly what height or point in the circuit you can consistently achieve a safe turn back.
Stay overhead
In CPL training, straight in arrivals and upwind departures are often introduced as students are encouraged to consider cost and flight time when operating. These can save time and some operators encourage them, but they often limit your options should power be lost. Most piston singles climb at a shallower angle than they can glide, and likewise most descend at a shallower angle than they can glide (to keep descent rates around 500 ft/min).
Many single engine operators dictate overhead departures and arrivals to their pilots in situations where a forced off airport landing is an unacceptable option, such as at night, in built-up areas or when water surrounds the airport. An example from my career is Lady Elliot Island (a small island off the coast of Bundaberg, Queensland), where operator Seair Pacific requires its Cessna Caravan pilots to arrive overhead at 2000 ft, a height that allows a safe glide approach after engine failure from before top of descent right through to turning final in the circuit.
Likewise, a wide orbit of the island after departure allows the aircraft to glide back and land on the island all the way through to top of climb, by which point a glide to the mainland is also possible. At a cost of a few minutes per flight, the aircraft is almost completely protected against going swimming should the engine quit.
Get high
While having a functioning engine is great, when you don’t have one, the next best thing is height, and lots of it. Height buys range but also time. The Pilatus PC12 shows how powerful this can be. From its service ceiling of 30,000 ft the PC12 can glide more than 75 nm in still air and stay airborne for almost 30 minutes. This nearly guarantees an airfield is in range and gives the pilot enough time to complete checks as well as plan their approach.
Ideally, every single engine aircraft would cruise in the upper flight levels. The constraints of aviation of course prohibit this. Airspace, weather, winds and supplemental oxygen requirements often keep most piston singles well below 10,000 ft. Performance limitations (or misunderstandings of) can push pilots to cruise even lower.
There are plenty of myths surrounding engine performance, but I’d like to tackle two: the perception that TAS decays significantly above full throttle height for normally aspirated engines, and the perception that the high RPM settings that fixed pitch propeller aircraft require to fly at higher levels somehow drastically damage the engine. Fresh out of flight school I certainly believed both.
The Cessna 172 is my favourite example of how these assumptions can be wrong. Flight levels aren’t generally associated with the Cessna 172, and yet its ceiling of 14,000 ft does allow small forays into the world of a standard altimeter setting. From personal experience (and with the assistance of supplemental oxygen), I can tell you that Cessna 172s perform fantastically at FL130. Digging into the Flight Manual, the numbers back this up:
Cessna 172S ~65% Cruise Performance at 2550 lb GW, ISA conditions | |||||
Pressure alt | RPM | %BHP | TAS | Fuel flow (L/hr) | Glide range to SL |
4000 | 2500 | 69 | 115 | 35.9 | 6 nm |
6000 | 2500 | 65 | 114 | 34.0 | 9 nm |
8000 | 2600 | 68 | 119 | 35.5 | 12 nm |
10000 | 2650 | 68 | 120 | 35.5 | 15 nm |
12000 | 2650 | 64 | 119 | 33.6 | 18 nm |
The concerns over a decay of airspeed as the air thins out are simply unfounded, with TAS only starting to decrease (by a whole 1 knot) at FL120. The engine will be running at a higher RPM and eventually require wide open throttle, however due to the reduced air density you’re still only producing cruise power. Cylinder head temperatures, exhaust gas temperatures and oil temperature will all still be well within limits, and the modest increase in engine RPM isn’t going to miraculously destroy the engine or shorten its life significantly. Every measure of performance (TAS, fuel flow and glide range) is better at 10,000 ft than it is at 6000 ft.
Important to note from the above table is fuel flow, with substantial fuel savings at higher levels. In saving fuel you’re less exposed to fuel exhaustion, a common cause of engine failure in all categories of aircraft.
This is only one aircraft and engine installation, so look at Section 5 in the Flight Manual of your aircraft and reconsider using higher levels. In the absence of previously discussed limitations or a short sector length, often A085 or A095 provide the best performance. If not, performance at these levels is so comparable to lower levels that the slight reduction in TAS is easily acceptable, given the significant increase in gliding time and range offered.
Thinking pilots
My most recent check captain said to me during a proficiency flight: ‘We want thinking pilots.’ The reason we can react to novel situations as pilots is because we think. Common to all strategies listed in this article is forethought—taking the time to anticipate where your flight is exposed to risk and then positively taking action to mitigate it.
Like in so many aspects of aviation, we as pilots plan for contingency. Some contingencies are easier to think about than others. Weather diversions, traffic delays, lighting failures—all give the pilot opportunity to put a plan into action and save the day. In contrast, engine failure often robs the pilot of this chance, with a destroyed aircraft but surviving passengers sometimes being the best outcome on offer. Perhaps this contributes to an apathy that can surround thinking about it.
Although reassuring, the statistics on engine failure don’t give licence to assume engine failure in a single won’t happen to you. Rather than passively waiting for power loss and falling back on trained responses, pilots must actively defend their aircraft against the consequences of engine failure. Know your aircraft and procedures. Fly as high as practical, keep your options open and have a clear plan rehearsed for engine failure during every sequence of flight.
Fantastic article that should be mandatory reading for all GA pilots.
I agree with Warren – a thoughtful and thought provoking article.
Yes, a great article with many good reminders, thank you. While I agree with your comments regarding cruising altitude in a fixed-pitch, normally aspirated single like a C-72, I would submit the “overruling” factor is not so much TAS or fuel flow but rather wind. While you can have great tailwinds at altitude, I find in most cases wind drives me to fly lower than the zero-wind optimal A095 or A085 in a plane without supplemental oxygen.
And it always seems like we get headwinds in both directions doesn’t it!? A fantastic point though – the stronger winds of higher levels are often a reason to stay low. Thanks for your feedback.
Excellent..A must read.
Good article thanks.
Fortunately I’ve never had a complete engine failure in 1,500 hrs, although I’ve had varying degrees of partial power loss due to: (a) carb heat issues (b) blocked injectors – x4 (c) cracked cylinder (d) burnt exhaust valves x2 (e) faulty manifold valve (f) induction leaks, (g) magneto.
Great read – thanks for putting it together and making it so readily understandable.
Learn how to operate properly at any level, and the fuel burn will be way better than those book values. The C172 example above is 20% over optimum. Imagine how much fuel margin that buys? And only a 2-3 knots speed loss. FL120-150 is a nice place to be. I use it whenever practical. Particularly when crossing Bass Straight.
Learn how to understand your engine monitor. 99% of piston pilots are like dogs watching TV. And I am not joking. This is serious. Many engine failures, including all those commented by Peter above can be dealt with by using the information on an EMS, but you need to know what it is telling you. Valve failures can be seen 10-50 hours prior to the failure. Magneto’s and ignition parts. Sadly none of this is taught in flying training and many wrong things are taught, and required to be learned wrong in order to pass CASA exams.
Great article by the way!
Very few 172 drivers are going to get anywhere near FL120 & above! That’s just fairytale stuff for most Pvt pilots out there going for a jolly even a long one! Not many 172S’s out there either that Pvt pilots own or hire, in the real world most of the above is impracticable! Weather/winds often preclude that sort of stuff VFR!
With 40 yrs driving planes under my belt from C150 thru to Buses I’ve never had a complete failure or damaged an engine & most of it done well before all the feel good stuff that’s available these days. These days I drive my own plane using those 40 years behind me & avoid situations (mostly) where an engine failure will hurt me. Hearing someone flying a Jab over Tiger country makes me cringe! Their life I guess!
The turn-back stunt is always an interesting discussion, a killer mostly!
Anyway mostly a good article but some away with the fairy’s:-)
Lots of 172S and 172SP aircraft are available to private pilots to rent in North America, and most of the big training centers use the S or SP model. I do agree with some of it being impractical and engine failures in singles are very much drilled into students pilots to the point where it’s over taught, especially since most accidents occur due to loss of control.
Walter : I din’t always go along with some of your previous comments.But on this subject I have your back.FL120,in a C172 or even a PA28,,is fairytale stuff,even when crossing Bass Strait.Like yourself I came up with none of this fancy engine management gear that is available now.The good old fashioned ear,and a sound knowlege of my aircrafts capabilities,and engine management practices has kept me out of trouble.As far as crossing Bass Strait,I do it on a regular basis,In the Flight Levels “yes”,but I am operating a Beech Kingair’,PC12.,Learjet,or Cessna Citation ,
Hey Walter and Raptor!
Thanks for taking the time share your thoughts. I 100% agree that weather and winds are often reasons to not get up high, and flight levels without supplemental oxygen are also not feasible.
The message I was hoping to convey in that last section was that many aircraft perform much better than you might think up high, including normally aspirated pistons. I’m also personally quite skeptical of POH figures, so take a look at the image linked below – taken by myself in a Cessna 172S at FL130, hired out of Jandakot.
https://ibb.co/8XK0zV2
As for turning back – with you there as well. Certainly a killer if done too low or without preparation, so all the more reason to think about it before being forced to make the choice for real.
Interesting Read. Nice one Nic
Very interesting, a must read for all pilots.
Thanks for sharing.
[…] Reviewing general aviation in the US fleet between 1984 and 2006 (from NTSB annual reviews), the average fatal accident rate of single piston engine aircraft sits at 1.63 fatal accidents per 100,000 flight hours, compared with 1.88 fatal accidents per 100,000 flight hours in their multi piston engine cousins. via […]