Technology can assist, but not replace, human thoroughness in controlling this foreign object damage hazard
Aircraft maintenance is an unforgiving way to make a living.
As James Reason and Alan Hobbs say in their book, Managing maintenance error: a practical guide, ‘If some evil genius were given the job of creating an activity guaranteed to produce an abundance of errors, he or she would probably come up with something that involved the removal and replacement of large numbers of varied components, often carried out in cramped, ill-lit spaces, with less-than-adequate tools, and usually under severe time pressure.’
Leaving tools or fasteners in the component or system being serviced comprises about 10 per cent of maintenance error, Reason and Hobbs discovered. Like other categories of human error, losing tools is better controlled by systemising than by moralising. And the good news is that systems and technologies exist to control it. They are a better solution than relying solely on individual diligence which, as Reason and Hobbs point out, already has too many enemies in the hangar.
Stowaways and saboteurs
Lost tools have often resulted in embarrassment and expense, and sometimes in tragedy.
- On 23 October 2020, a Jetstar Airways Airbus A320 was taking off from Brisbane when the crew reported feeling a vibration and hearing a ‘popping’ noise that rapidly increased in frequency and volume. At the same time, the aircraft veered to the right of the runway centreline despite the first officer applying full left rudder. The captain immediately selected reverse thrust and brought the aircraft to a stop. During the incident, passengers, an air traffic controller and the crew of the following aircraft saw a burst of flames coming from the right engine. An inspection immediately after found metallic debris in the tailpipe of the right engine. When it was dismantled, a screwdriver tip was found in the engine’s combustion section. It had done significant damage to the high-pressure compressor. Based on the aircraft’s maintenance records, the tip had been in the engine for 112 flights. It nicked and scratched stator vanes and compressor blades, one of which eventually detached, causing the engine failure.
- On 3 November 2015, a Eurocopter AS365 N3 Dauphin landed after a maintenance test flight at Jandakot Airport with chunks missing from the leading edges of one rotor blade. A spanner was found 43 metres away on a taxiway. The Australian Transport Safety Bureau (ATSB) determined it had been left in the rotor head area and was likely ejected during the aircraft start up.
On several occasions we
didn’t go home until the
tool was found.
- On 28 February 1998, just after take-off, the crew of a Boeing 767 heard a series of loud bangs and the right engine exhaust gas temperature indicator rose rapidly into the red range. The right thrust lever was retarded to idle and temperature indications returned to normal. The crew declared an emergency, returned to the airport and landed safely. When the engine was removed for further inspection, a replaceable Philips screwdriver tip was found in its core. It was the first flight after the aircraft had undergone an ‘A’ maintenance check.
- Other accidents and incidents include a torch left in a Boeing 737-300’s wheel well that became lodged in the landing gear mechanism, preventing the pilot from raising the undercarriage; a Boeing 747 where the undercarriage failed to retract because a pair of pliers had been left in the right body gear-up lock during maintenance; and a bent screwdriver found in the wreckage of a Vickers Viscount that crashed in Northern Ireland in 1957.
Tools don’t have to be left inside an aircraft to damage it. The ATSB found tools and equipment were the second most common cause of foreign object damage (FOD) reports, accounting for about 19 per cent of cases.
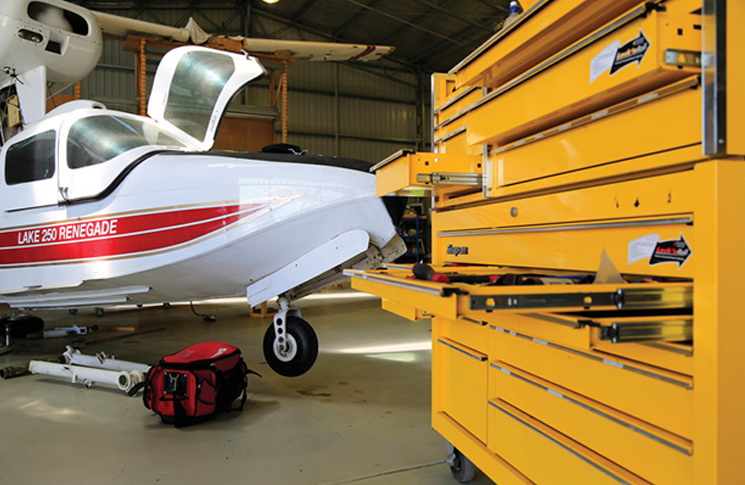
A place for everything: solutions
Tool control is any system that monitors where tools are and/or who is using them. Its guiding principle is that all tools be returned at the end of the day or job.
‘The reason we have tool control is so loose tools don’t provide an extra hazard to the aircraft environment,’ Esso Australia Aviation Safety Manager Mike Hutchinson says.
There are 2 distinct schools of thought on tool control. Strict centralised tool control is a tradition in military aircraft maintenance where no private tools are allowed and everyone shares a central tool kit, known as a crib. In civilian operations, engineers and technicians have traditionally used their own tools.
‘I started in the navy, which had a quite rigorous tool system,’ CASA Senior Engineer Maintenance Gustav Anderson says. ‘Every time a job was opened on an aircraft, the tool control room would open and you would ask for each tool you needed. As you got your tools, dog tags accumulated under your name and at the end of the day these had to be cleared and signed off. On several occasions we didn’t go home until the tool was found.’
CASA says relatively little about tool control specifically but instead focuses on the safety standards that must be met in aircraft maintenance. Civil Aviation Advisory Publication 30-04 v3.0 August 2020 says, ‘Tools and equipment should be controlled so that their location is always known. There should be a procedure to ensure that at shift changes, or when aircraft leave the organisation, all tools and equipment are accounted for.’
Since the introduction of CASR Part 145 for approved maintenance organisations in 2013, more civilian operators of complex aircraft have adopted the centralised military-style approach. This can be done in several ways, either with variations of the military crib and tag system, or with the aid of technological systems.
Hutchinson, whose job is to assure safety in maintenance and operation of 5 AgustaWestland 139 helicopters flying to Bass Strait oil platforms from Longford in Victoria, says the days of an engineer working on a large complex aircraft bringing their own toolkit to work are gone.
‘If you are a Part 145 organisation, you will have tool control procedures listed in your exposition,’ he says. ‘How you issue tools, monitor tools, how toolboxes work – all that needs to be clearly documented in the exposition.’
Tool control methods include:
- Shadow boards – these display the outline of any missing tools
- Shadow boxes – these use foam cut-outs to hold tools securely and also display the outline of missing tools.
- Tool folders/pockets – these have a pocket for each tool and so indicate missing tools
- Tool tags – this involves tokens being issued with the tools but kept in the tool store or crib under the borrower’s name. Tools are exchanged for tokens on return and all tokens must be cleared at the end of the job or day.
- Barcoding – where a tool is checked out to a known person using the same technology used at point of sale in supermarkets. Personal barcodes can also be used to control access to toolboxes and cribs.
- Radio frequency identification (RFID) – involves tools being tagged with RFID chips. These are used to simplify check-out and return of tools.
- Colour coding – may be used in conjunction with any of these systems to allow tools to be more easily seen and removed from a job and to identify if tools are missing from their storage.
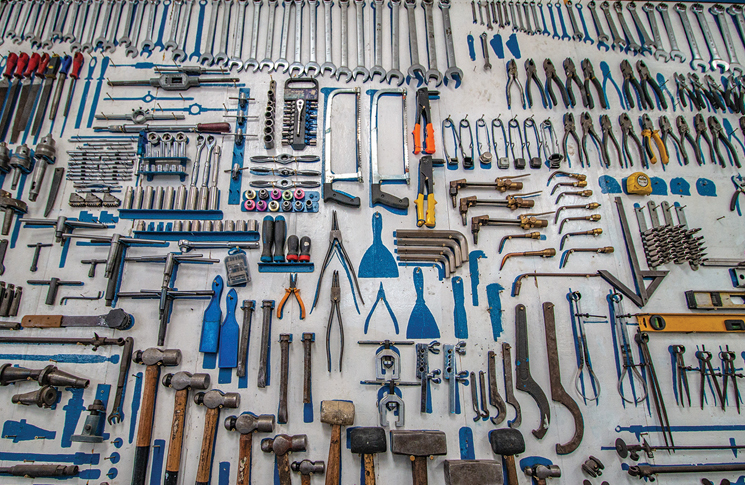
Hutchinson describes another aspect of tool control – calibration. Some of the tooling is calibrated – things like torque wrenches which fasten to a specified tightness or ‘torque’. ‘The calibration of those needs to be tracked, and that comes under tool control,’ he says. ‘It’s about assuring all fasteners are tightened to specification and, should one of your wrenches go out of calibration, you need to know what aircraft it has been used on, and when.’
Industrial hand tool manufacturers including Snap-On of the USA, Stahlwille of Germany and Facom of France offer tool control systems as part of their product range. In addition, tool control specialists including Xerafy of China, Cribmaster of the USA and the British firm Coplan offer systems based on combinations of information technology and customised storage. An Australian firm, Henchman Products based in Newcastle, and Minneapolis, USA, also trades in this field. Its specialty results from the tool supplier’s proximity to RAAF Williamtown, which became an early customer and introduced Henchman to the military’s emphasis on strict tool control.
Our aviation customers are specifically interested in safety, and, for them, cost isn’t as much of an issue.
Henchman offers 3 products in its HenchmanTrak electronic tool control system, all of which use the same recording and reporting software.
- KabTrak is a tool cabinet that uses pressure sensors to detect when a tool has been removed. A RFID card or fob is required to open the cabinet, which identifies each user. The cabinet control panel has a green display if all tools are returned, or red if some are missing. This can also be monitored remotely and email alerts can be sent to supervisors.
- CribTrak is a barcode/RFID scanning system for issue of tools from centralised cribs. The user must scan their RFID card, enter details of the aircraft they are working on and scan the tool or kit.
- PortaTrak is a system that uses sensitive scales to issue and return toolboxes, comparing their weight on each occasion. Access control is similar to the other 2 systems and the scales can detect differences of 4 grams, less than the weight of a drill bit or power screwdriver tip.
Henchman products general manager Blake Beatson says the company has customers in aviation, biomedical, rail transport and corrections. Systems start at about $20,000 and are custom-made.
‘Our other customers are interested in controlling lost tools, theft and increasing productivity, with safety as an additional benefit, but our aviation customers are specifically interested in safety and, for them, cost isn’t as much of an issue,’ Beatson says.
Esso Australia have invested in a Snap-On level 5 tool control system, using 4 camera-recognition tool cabinets and an aircraft management system to monitor use and calibration of specialist tools. Hutchinson says this must be seen in the context of a multimillion-dollar investment in aircraft, personnel and facilities. ‘We have introduced a user-friendly system that at the end of the day was a great investment,’ he says.
But discipline, commitment and integration into an organisation’s safety management system (SMS) are at least as important as technology in tool control, Hutchinson says.
‘To be quite honest, a shadow board works really well and is a low-cost investment,’ he says. ‘A photo recognition toolbox works well too, but in both cases, ultimately there’s a human in the system and they need to be motivated and diligent.’
A vital part of Risk Management and Continuing Airworthiness for the Aerospace Engineer.