Gliding a powered aircraft is a rare and high-stakes exercise. If you have to get down safely without engine power, knowledge and experience will be your only friends
Many articles cover in-flight engine failure – establishing glide speed, checklists for engine restart, choosing an off-airport landing spot – but few describe techniques for the glide itself.
This article focuses on the control aspects that permit us to do everything else: how to glide, how to transition from glide to engine-out landing and how to safely practise these things so you’ll be ready when engine failure happens to you.
Whatever aeroplane you’re flying, make sure you know the steps required to get the best glide performance at the best glide speed.
Kind of a drag
Best glide speed (VBG) is the indicated airspeed at which the aeroplane travels the greatest horizontal distance for the amount of altitude lost. The speed will vary by aircraft type and even changes with aeroplane weight. Look for VBG in the speeds for emergency operation at the beginning of Section III of a Pilot’s operating handbook (POH) or Aeroplane flight manual (AFM) and on the glide checklist in the Emergency procedures.
As well, best glide speed is the indicated airspeed at which the aeroplane develops the least amount of drag. Aerodynamic drag comes in 2 forms: parasite drag – or air resistance –and induced drag – drag created as a by-product of lift development. Parasite drag begins at zero airspeed and increases with the square of airspeed. Induced drag begins at the speed at which lift begins to generate and decreases with the square of the airspeed. Plot the 2 and then the sum of parasite and induced drag for a given airspeed and you have the total drag curve (Figure 1).
Glide ratio
But how far can you glide? Most POHs and AFMs provide an expectation of glide performance. Sometimes this is expressed as altitude lost for forward distance. These expectations are based on an aeroplane on its least-drag airspeed, in its least-drag condition (gear, flaps, cowl flaps and/or propeller speed as applicable), flying wings level in coordinated flight. Any change to airspeed or configuration, any slip or skid or even a coordinated turn, and the performance will be less than the handbook predicts.
The glide ratio is used to draw a ‘glide ring’ around the aeroplane in EFB software. The glide ring illustrates the aeroplane’s maximum gliding distance, considering altitude, winds and terrain elevation. This helps a pilot constantly monitor options in anticipation of engine failure and make decisions about where to aim after a power loss occurs.
The software assumes the published glide ratio for the aircraft type; some software requires the pilot to input this ratio during set-up.
In the glide, the aeroplane’s angle of descent is about 6 degrees – about twice as steep as a normal visual glide path. Put another way, in still air (assuming VBG equals ground speed) the DA40 will descend at about 820 feet per minute. The C172S will descend at about 760 feet per minute. The Bonanza will descend at about 950 feet per minute in the best glide configuration – almost twice the rate of descent of a normal landing. In all 3 cases, the glide is just a little steeper and at a slightly greater rate of descent than you’d see in an aggressive short-field landing.
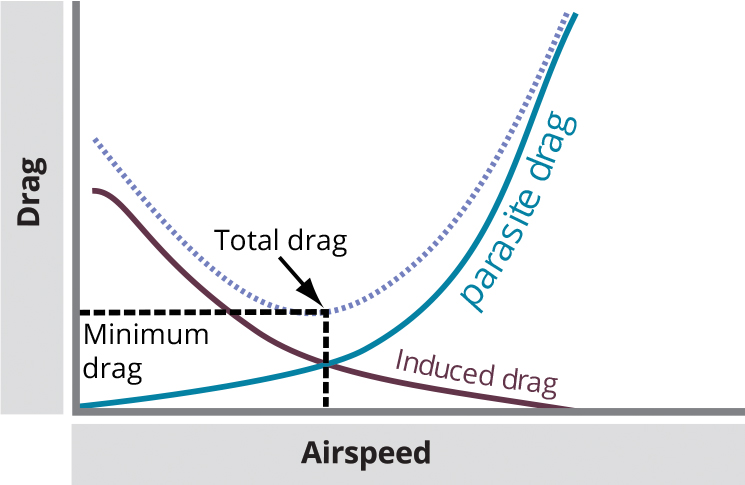
Configuration
If power equals zero, the rest of the performance equation depends on drag. The POH/AFM details the proper configuration for maximum glide. In retractable gear aeroplanes this is almost always ‘gear up’. Flaps are almost always fully retracted; if the aeroplane has cowl flaps, they should be closed to reduce drag as well.
Aeroplanes with controllable-pitch propellers have another vital component to least-drag configuration. A propeller in fine pitch (high RPM) presents the flat propeller blades to forward flight, giving it the highest drag. Some – but not all – aeroplanes with controllable-pitch propellers call for moving the propeller to full-coarse pitch (low RPM). Low RPM has a higher angle of attack in the direction of propeller rotation but also streamlines the propeller blade somewhat to the forward direction of flight, reducing total parasite drag. It’s the closest we get to feathering a propeller in most single-engine aeroplanes.
I demonstrate this to pilots in the Bonanza. At a safe altitude, I reduce throttle to idle to simulate total engine failure and ask the pilot to establish and maintain VBG. Once established, I ask the pilot to tell me the vertical speed. At typical training weights this is usually about 1700‑1900 feet per minute and takes a roughly 5 degrees nose‑down attitude. I then have the pilot talk through the engine restart checklist and, assuming it does not restart, direct him/her to ‘commit to glide’, that is, pull the propeller control to low RPM. The result is probably the greatest acceleration you’ll feel in an A36, from the reduction in drag; VBG requires raising the nose to about level attitude and the result is a 700 to 900 fpm rate of descent – an approximately 50 per cent improvement in glide performance from the simple act of reducing propeller speed. Then I direct extending the landing gear. With gear down and prop coarse, VBG requires putting the nose back down 5 degrees and results in 1700‑1900 fpm downward – cruise RPM prop drag is as great as the drag of landing gear. This demonstration is often the first thing a pilot says when I ask later, ‘What impressed you the most about this flight?’
Whatever aeroplane you’re flying, make sure you know the steps required to get the best glide performance at the best glide speed.
Speed range
The drag curve is angle-of-attack (AoA) dependent – changes in AoA will change induced drag and may change parasite drag. As aeroplane weight decreases, the curve shifts to the left, to a slower airspeed. The weight-adjusted speed is following a mathematical formula. Some POHs/AFMs list different speeds for lighter weights.
VBG may be as much as 5 knots slower at the lowest practical aeroplane weight. If you find you’re a couple of knots slower than VBG, don’t worry, it’s probably helping. Fine‑tune your speed – time and workload permitting – to find ‘the best’ glide speed for the current weight.
If you’re high over a runway but not high enough to make another complete circuit, you can increase your descent rate by easing the nose downward and accelerating 5 knots or so. Fly the higher rate of descent until you’re in position to glide from your current location, then return to best glide speed. You could accomplish the same thing by slowing down, but often VBG is not too far above stalling speed. It’s better to have excess speed (extra energy) for a glide than to have too little energy by flying slower.
Glide’s end
The objective is to glide to a point from which a landing may be made. Since the rate of descent is steeper than a normal landing, and will increase in a turn, you’ll want to arrive in the circuit of your runway (or paddock) on downwind a couple of hundred feet higher than normal. From there you can make a nearly continual turn as needed to align with your landing surface.
If you have any doubt whether adding another 500 foot‑per‑minute rate of descent (typical with gear extension) will permit you to make it to your landing spot, land gear up.
If you find yourself high on finals you may add flaps, careful not to do so too soon so your well-planned glide doesn’t suddenly turn up short. Put retractable wheels down only when on very short final; in aeroplanes with a fast gear extension (like the Bonanza), I teach leaving the gear up until you’re past the last obstacle and have the beginning of the landing surface beneath you. If you have any doubt whether adding another 500 foot-per-minute rate of descent (typical with gear extension) will permit you to make it to your landing spot, land gear up. It’s better to slide on under control than to extend the gear and collide with obstacles or stall, trying to ‘stretch’ your glide.
Most POHs/AFMs also list a landing-without-power speed. This is often called the ‘least rate-of-descent’ speed. However, published landing-without-power speeds are usually a little faster than what an aerodynamicist might calculate. With power loss, a single-engine aeroplane also loses propeller blast over the elevators, even with the throttle at idle. The added airspeed provides the control authority required to arrest descent and flare for engine-out landing. The landing-without-power speed is even slightly faster than the normal landing speed at the same flap position.
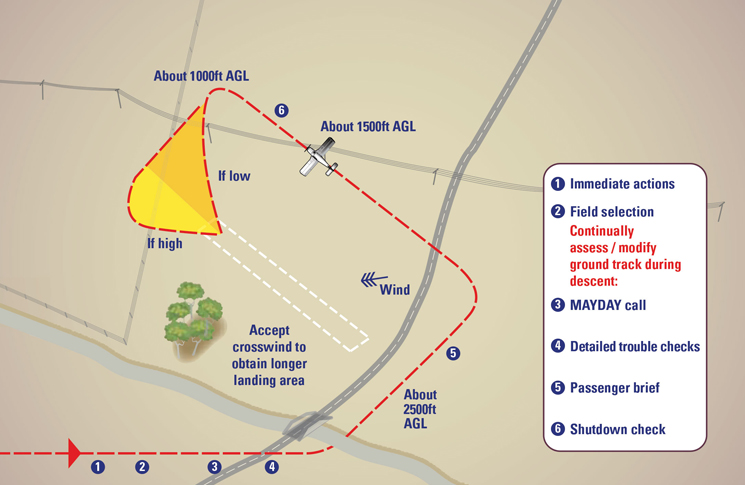
Practice
You won’t be successful at implementing these techniques without practice. Here are a few things you might ask your instructor to cover and include in your practice routine:
- Glide attitude demonstration. As I described about the A36’s propeller, simulate power loss at a safe altitude and determine the pitch attitude that results in best glide speed.
- Glide range visualisation. During glide practice, visualise your glide range. I teach pilots that the radius of a ring described by the aeroplane’s wingtips as seen from the cockpit is a close approximation of available glide distance. The greater your altitude, the further this radius describes. Don’t forget to look behind the wings for the best option.
- Speed check. From VBG, reduce speed 2 knots and see how the vertical speed changes. Do the same thing at 5 knots below VBG, and at 2 and 5 knots above VBG.
- Turn penalty. Establish best glide and note your vertical speed. Then see how much vertical speed increases in a turn at various bank angles. Get a feel for how much altitude you’ll lose in a 180-degree turn at what you consider to be a comfortable engine-out bank. This will tell you how high above terrain you must be on downwind to make it to your runway. It helps you predict how many 180-degree turns you can make from your current altitude to that downwind point.
- Gear and flaps. In a glide, get familiar with the changes in pitch attitude and vertical speed that result from flaps and/or landing gear extension.
- Power-off 180. The power-off 180 is a training manoeuvre that consists of pulling the power to idle on downwind abeam your intended touchdown spot, then gliding without adding any power to touch down accurately on a defined point on the runway. This is teaching you to make that engine-out circuit.
- Rounding out. Practise the transition from VBG to landing-without-power speed, including lowering the nose to attain landing-without-power speed as applicable.
- Short-field landings. The glide speed and rate of descent are similar to that of a short-field landing. Practise power-off short-field landings regularly to keep this sight picture and the timing of the flare in mind.
Glide profile
CASA describes the profile for an engine-out descent, along with actions to take along the way. All of this assumes you know how to glide, how to transition from glide to engine-out landing and how to safely practise these things so you’ll be ready when an engine failure happens to you.
Reminds me of a flight in a BA B747-400 into Sydney. The aircraft was very light (a short leg from Brisbane with relatively few pax) and ATC was applying aggressive speed control to maintain distance behind the preceding aircraft in the sequence. With throttles at flight idle and the assigned speed requirement reducing from 250 to 230 to 210KT in the space of a couple of minutes and still around F250, the plane did not want to descend. The captain (PM) who seemed to be mentoring the new-on-jets FO (PF) asked the FO how he planned to lose height but without using speed brakes. He provided a hint by asking the FO what the maximum gear extension altitude (not speed!) was applicable for that model of aircraft. We both learned something that day.
Thanks for such a good article. I believe a couple of other issues may be worth considering:
a) Recognition: Engine failure indications may be confusing – Manifold Pressure Might not change at all, RPM might just reduce a little, sound may not change much depending on power setting before the problem.
b) Training: Practicing glides in an aircraft with a fixed-pitch prop at idle power may give a false impression of ‘real world’ engine-out glide ratio. Consider a little flap in training to simulate the extra drag from a windmilling prop.